By Jay Palter | July 27, 2022
Turbulent economies, shrinking budgets, volatile labor markets, businesses have to contend with a lot of uncertainty today. So no wonder many are looking for ways to make operations more predictable and cost-effective.
Smart asset management strategies can help standardize and simplify some of your more volatile equipment-related costs. As a result, you’ll be able to make smarter purchases, extend the lifecycles of your most expensive equipment, and make equipment more available for essential operations.
This article explores how smart asset management technology can be a core component of your asset lifecycle management (ALM). We explore how best to structure an ALM program, show you how an equipment management system can fit within it, and even share some specific use case benefits.
What is an Asset Lifecycle?
But let us start with some fundamentals and clarify what an asset lifecycle is. For our discussion, an ‘asset’ is any physical object whose absence would have a meaningful impact on one of your workflows—for example, a handheld scanner in a distribution center. Employees need a scanner to carry out their work. If one isn’t available, charged, and functional, those workers are idle until they find a usable scanner.
An asset’s lifecycle includes every activity from the moment you decide you need to purchase it until you dispose of it. Or “from the cradle to the grave,” as we sometimes like to say.
Why put effort into lifecycle management?
The goal of managing each asset’s lifecycle is to maximize its availability and effectiveness and extend its lifecycle. Lifecycle management practices help you extract the maximum value possible from your assets at each point in their lifespan. They emphasize careful purchasing, regular maintenance, and managed use.
Asset Lifecycle Stages
The five practical stages of physical asset lifecycle management are:
- Planning
- Acquisition
- Use
- Maintenance
- Disposal
Once your lifecycle management program is in place, each new asset entering your organization should pass through all five stages. It often makes sense to conduct an inventory of existing assets, so you can integrate them starting with the Use stage. And while most assets spend the majority of their lifecycles in the Use stage, it is important to give equal effort to all five stages if you want to maximize asset value in the long run.
Here are the five stages explained in a little more detail. Organizations will want to craft policies and procedures for each stage to keep lifecycles as organized and predictable as possible. If you’re using an equipment asset management system, standardized digital processes also help you collect meaningful asset data, which can inform operations and future purchases.
Planning
Anytime an authorized decision maker decides new assets are needed, the Planning stage kicks off. First, you’ll research different assets on the market—or sometimes available through internal development—that will solve the problem in question. For major purchases, you may want to bring in stakeholders from different parts of your organization to weigh in on your potential investment. You may also want to conduct an internal review to ensure all stakeholders are on the same page about the problem you want to solve, its impact on stakeholders' operations, and the organization’s priority for resolving this problem.
Acquisition
Once your decision maker or team of stakeholders has identified the asset you want to purchase, you next need to acquire it. Why would that need its own lifecycle stage? Because acquisition involves more than just clicking the ‘place order’ button. For large or fragile assets, you may need to plan out how they will be delivered to your facility and how you’ll deploy them.
You also need to have an intake process to ensure each asset makes its way into your asset management system. You will at least want to inventory the asset and assign an owner within your organization who is ultimately responsible for it. You may also want to tag it for company equipment tracking and conducting employee training on its use.
Use
Now you’re ready to use your asset. Ideally, you will want a way to collect and measure the ongoing use of your assets. That is most easily accomplished using enterprise asset tracking features in a smart asset management system, but you could also capture meaningful data through manual tracking and record keeping. Try tracking details about asset use, like who uses it, when they use it, and what problems they report.
Maintenance
Identify a maintenance strategy that makes the most sense for each asset and have the asset’s owner schedule the relevant maintenance checks. Ideally, you’ll want to do this before the asset is released into general use.
For one asset, like a forklift, for example, you may want to schedule preventive maintenance, such as tire and battery replacements. For another asset, like a handheld scanner, you may want to schedule routine maintenance, like monthly software updates.
Disposal
Eventually, every asset will reach the end of its lifecycle. That is the point at which you can no longer extract enough meaningful value from the asset to justify its ongoing management and maintenance costs. At this point, you may have a few different options, depending on the nature of a given asset.
You might be able to recoup money from some, such as by selling retired fleet vehicles. You will need to dispose of others according to industry, environmental, and governmental guidelines. The final event in your equipment lifecycle management workflow is to evaluate whether a replacement purchase is necessary. If so, simply launch a new asset lifecycle from the Planning stage.
What is a Smart Asset Management System?
You can use a smart locker system for ALM. Smart lockers self-manage stored assets, freeing up staff for more productive work. Smart lockers can track when employees sign out or return assets and how your employees use them. Smart automation software can also enable new workflows.
Several core components are needed to make a company asset management system “smart.”
Storage lockers
At the core of a smart locker system is the storage lockers. These lockers hold idle equipment and charge electronic devices, so they’re ready when your employees need them next. Some company equipment management systems are one-size-fits-all. Others, like the AssetTracer system from Real Time Networks, are modular. You can combine different cabinets into the configuration you need to fit your gear within the footprint you have to work with.
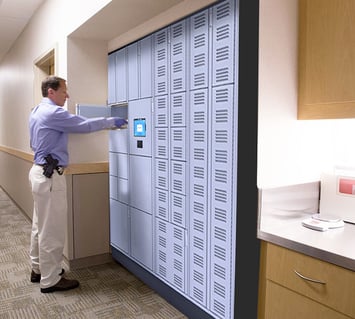
Smart panels
Attached to each set of lockers is a smart access panel. Users authenticate themselves here and respond to any checklists you want to present to them at signout or return. Once complete, the panel unlocks only the cabinets you want to give the users access to.
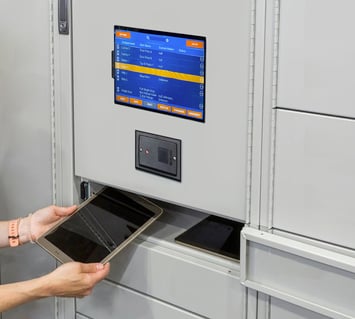
Content surveillance
You can attach RFID tracking tags to each stored asset. Then content surveillance sensors in the lockers can verify that employees take and return the correct items when they request access. RFID is a low-power, short-range wireless standard that works through plastic, so you can even scan multiple kit components simultaneously. You can also get device information over some wired USB connections if you plug electronic devices in to charge.
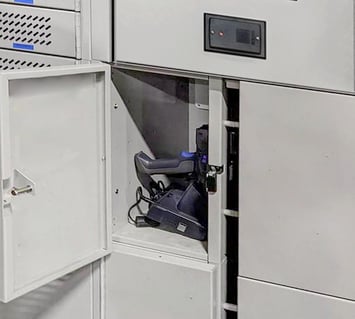
Management dashboard
All the data collected from the smart locker system feeds back to a central management dashboard. In AssetTracer systems, you access the dashboard through a secure web app on authorized PCs, phones, or other mobile devices.
This dashboard allows you to monitor asset use in real time, manage users, and generate reports for your budget planning or regulatory compliance. In addition, these dashboards provide a complete picture of every asset’s lifecycle.
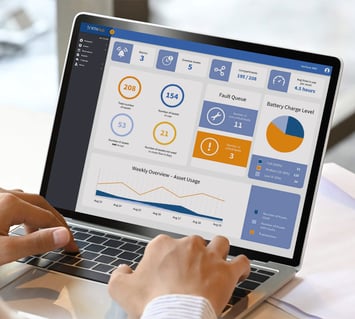
Key Benefits of Asset Lifecycle Management Using a Smart Equipment Management System
Managing your asset lifecycles using a smart locker system offers several benefits. Some of the most significant seen by many organizations include:
Improved operating efficiency
Smart lockers automate a broad range of time-consuming work. Managing asset transactions alone is often a full-time position within many organizations. Smart lockers automate that process and perform it consistently without human error. They never get tired, need a mandated break, or go on vacation. And you can instantly update locker systems with new users and access permissions in seconds, so everyone always has access to what they need to do their job.
Reduced costs
Efficient operations, better-managed lifecycles, and automatically-enforced maintenance schedules contribute to reduced operating costs when using a locker system.
Better informed decision-making
By managing your assets from the cradle to the grave, you’ll almost certainly uncover new insights about their use and your wider business operations that you wouldn’t otherwise. For example, one of Real Time Networks’ manufacturing customers discovered that warehouse employees were hoarding those handheld scanners we mentioned earlier.
Before using an AssetTracer system, this company had no central lifecycle management for its scanners. Employees grabbed their favorite known-working devices and hid them around the warehouse so no one else could steal them. It turned out this company was massively overspending on replacement scanners because so many were going missing. Thanks to implementing digital ALM via an AssetTracer system, this company drastically reduced its annual expenditure on new handheld devices.
Extended asset lifecycles
Real-time asset tracking allows you to make better decisions about maintenance schedules that will maximize your asset’s lifecycle. You can also use a physical asset management system to control which assets employees sign out in a given order. For example, you can randomly rotate signouts of mobile devices to distribute wear-and-tear across your entire inventory. Or you could distribute according to the longest held, meaning employees would always receive the most-charged device.
Decreased downtime
Sticking to maintenance schedules with the support of an asset locker system will help reduce unexpected downtime, as will built-in charging. You also reduce waiting time. Employees can sign out the equipment they need in seconds. No more waiting in line at the beginning of a shift to receive the gear they need to do their jobs.
ISO 55000 support
If your organization follows ISO 55000 asset management standards, an automated smart locker system can help you maintain compliance. You’ll automate record keeping and reduce errors thanks to electronic management tools. And you’ll gather data that can inform the steady improvement of your ALM program.
Still not sure what smart locker solution you need?
Contact Real Time Networks today for a FREE 30 min consultation.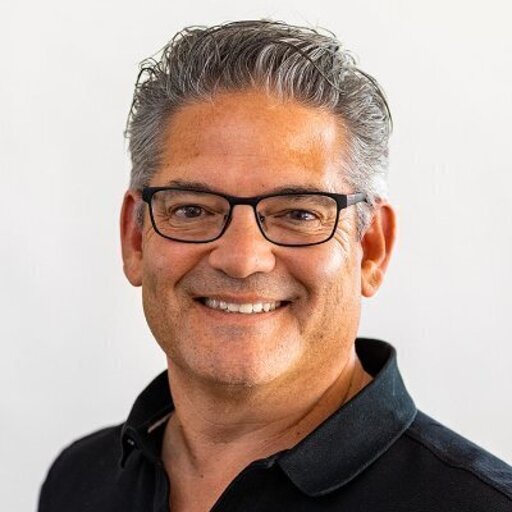
Jay Palter
Vice President of Marketing